What cable machinery for 11 and 33 kv cable manufacturing?
1. Cablespecification below:
Single cores:
- 1 KV XLPE SINGLE CORE ALUMINIUM CONDUCTOR CABLES
- 11 KV XLPE SINGLE CORE COPPER CONDUCTOR CABLES
- 12.7/22 KV XLPE SINGLE CORE ALUMINIUM CONDUCTOR CABLES
- 12.7 / 22 KV XLPE SINGLE CORE COPPER CONDUCTOR CABLES
- 19 / 33 KV XLPE SINGLE CORE ALUMINIUM CONDUCTOR CABLES
- 16 - 19 / 33 KV XLPE SINGLE CORE COPPER CONDUCTOR CABLES
- 33 / 33 KV XLPE SINGLE CORE ALUMINIUM CONDUCTOR CABLE
- 33 / 33 KV XLPE SINGLE CORE COPPER CONDUCTOR CABLE
Three cores:
- 11 KV XLPE SINGLE CORE ALUMINIUM CONDUCTOR CABLES
- 11 KV XLPE SINGLE CORE COPPER CONDUCTOR CABLES
- 12.7/22 KV XLPE SINGLE CORE ALUMINIUM CONDUCTOR CABLES
- 12.7 / 22 KV XLPE SINGLE CORE COPPER CONDUCTOR CABLES
- 19 / 33 KV XLPE SINGLE CORE ALUMINIUM CONDUCTOR CABLES
- 16 - 19 / 33 KV XLPE SINGLE CORE COPPER CONDUCTOR CABLES
- 33 / 33 KV XLPE SINGLE CORE ALUMINIUM CONDUCTOR CABLE
- 33 / 33 KV XLPE SINGLE CORE COPPER CONDUCTOR CABLE
2. Main feature of 11 to 33 kv cable:
Thespecifications for 11 kV and 33 kV cables can vary depending on the specific
requirements and standards followed in different regions. However, here are
some general specifications for 11 kV and 33 kV cables:
11 kV Cable:
- Voltage Rating: 11 kilovolts (kV)
- Conductor Material: Copper or Aluminum
- Conductor Size: Typically ranging from 16mm² to 630 mm²
- Insulation Material: Cross-linkedPolyethylene (XLPE) or Polyvinyl Chloride (PVC)
- Insulation Thickness: Varies based on thecable size and application, generally ranging from 3 mm to 20 mm
- Sheath Material: Polyvinyl Chloride (PVC)or Polyethylene (PE)
- Sheath Thickness: Varies based on the cablesize and application, typically ranging from 1 mm to 3 mm
- Overall Diameter: Depends on the cablesize, insulation thickness, and sheath thickness
33 kV Cable:
- Voltage Rating: 33 kilovolts (kV)
- Conductor Material: Copper or Aluminum
- Conductor Size: Typically ranging from 35mm² to 1000 mm²
- Insulation Material: Cross-linkedPolyethylene (XLPE) or Ethylene Propylene Rubber (EPR)
- Insulation Thickness: Varies based on thecable size and application, generally ranging from 5 mm to 40 mm
- Sheath Material: Polyvinyl Chloride (PVC)or Polyethylene (PE)
- Sheath Thickness: Varies based on the cablesize and application, typically ranging from 1.5 mm to 4 mm Overall Diameter: Depends on the cablesize, insulation thickness, and sheath thickness. These specifications are provided as ageneral guideline, and it's important to consult the relevant standards and local regulations specific to your region to ensure compliance with the required specifications for 11 kV and 33 kV cables.
- Additionally, cable specifications can be customized based on specific project requirements, environmental conditions, and industry standards.
11 to 33 kv cable specification
- The specifications for cables with voltageratings ranging from 11 kV to 33 kV can vary based on specific requirements and standards. Here are general specifications that cover this voltage range:
- Voltage Rating: 11 kV to 33 kV
- Conductor Material: Copper or Aluminum
Conductor Size:Typically ranges from 16 mm² to 1000 mm²,depending on the application and current-carrying capacity needed.
Insulation Material:Cross-linked Polyethylene (XLPE) iscommonly used for medium voltage cables. It provides excellent electrical insulation properties and thermal stability.
Insulation Thickness:Varies based on the cable size, voltagerating, and application. Generally ranges from 3 mm to 40 mm to meet the required electrical and thermal insulation requirements.
Metallic Shielding (if applicable):For cables requiring shielding againstelectromagnetic interference (EMI), metallic shielding in the form of copper or aluminum tape or wire braid may be applied around the insulation layer.
Sheath Material:Polyvinyl Chloride (PVC) or Polyethylene(PE) are commonly used for the outer sheath. They provide mechanical protection, resistance to moisture, and environmental protection.
Sheath Thickness: Varies based on the cable size, voltagerating, and application. Typically ranges from 1 mm to 4 mm to provide appropriate mechanical and environmental protection.
Overall Diameter:The overall diameter of the cable dependson factors such as conductor size, insulation thickness, metallic shielding (if present), and sheath thickness. Thesespecifications provide a general overview, and it's important to consult relevant standards, regulations, and project requirements specific to your region and application. Local standards and regulations, such as IEC, ANSI, or specific national standards, should be followed to ensure compliance and safety.
Additionally, cable manufacturers or suppliers can provide more detailed specifications and guidance based on your specific needs and application requirements.
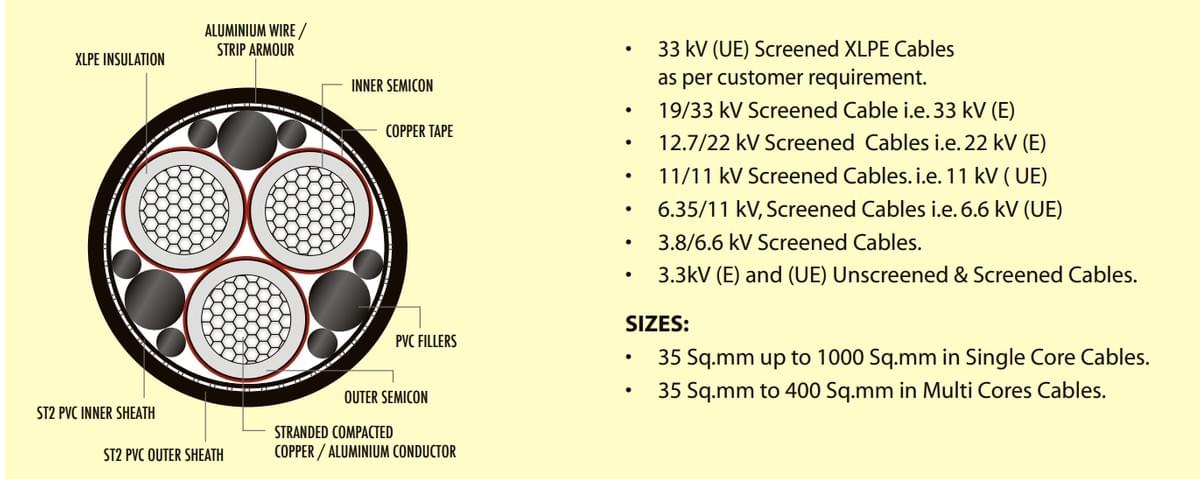
3. Machineslist for manufacture:
- Copper or aluminum conductorbreakdown rod machine for from 8 or 9.5 rod drawing to 1.5-5mm wire.
- 630/1+6+12+18+24 rigid stranding machine: twisting for 10 to 1000mm2 copper and aluminum conductor
- 90 or 120 cable extrusion line:produce 10 to 150mm2 cable insulation layer, An extrusion machine that melts
and processes the insulation material, such as Polyvinyl Chloride (PVC) or Cross-linked Polyethylene (XLPE), and applies it around the conductor wires to form the insulation layer of the cable.
Bow type laying-up machine 1250/1+4: adopt below 95mm2 insulation wire, speed is faster upto 160m/min.
Cradle laying-up machine 1600/1+1+3: adopt 4x300mm2 insulation wire.
- 6-33 LV CCV Line: refers to aContinuous Catenary Vulcanization (CCV) Line used for the production of
Low-Voltage (LV) cables with voltage ratings ranging from 6 kV to 33 kV and utilizing Cross-linked Polyethylene (XLPE) as the insulation material.
Drum twister machine 3150mm +4x2500 pay-off with steel tape and steel wire armouring function. Like 4x400
etc.
- 150 cable sheathing machine:produce big cable sheath.
How to choose 11 to 33kv cable machinery:
Choosing the right machinery formanufacturing 33kV cables involves considering several important factors. Here are some key points to consider when selecting 33kV cable machinery:
Capacity and Output: Determine theproduction capacity required for your specific needs. Consider factors such as
the expected production volume, cable sizes, and types (such as single-core or multi-core cables). Ensure that the machinery can handle the desired output and meet your production goals.
Cable Specifications: Understand thespecific requirements of 33kV cables you intend to manufacture. Consider
parameters such as conductor size, insulation material (e.g., XLPE or EPR), shielding requirements, and any additional layers or features required for the cables. Ensure that the machinery can handle the desired cable specifications
and meet relevant industry standards.
Quality and Reliability: Look for machineryfrom reputable manufacturers with a track record of producing high-quality equipment. Consider factors such as machine durability, reliability, and the availability of spare parts and technical support. Quality machinery will help ensure consistent and reliable production of high-quality cables.
Flexibility and Customization: Considerwhether the machinery allows for flexibility and customization to adapt to
different cable variations and future market demands. Look for machines that offer adjustable settings, modular components, and the ability to accommodate various cable designs and sizes.
Automation and Technology: Evaluate thelevel of automation and technological features offered by the machinery.
Advanced features such as computerized control systems, data monitoring, and remote diagnostics can enhance productivity, efficiency, and quality control.
Safety Features and Compliance: Ensure thatthe machinery meets safety standards and regulations. Look for features such as emergency stop buttons, safety guards, interlocks, and compliance with relevant electrical and safety standards.
Cost and Return on Investment (ROI):Consider the upfront cost of the machinery and weigh it against the expected return on investment. Evaluate factors such as production efficiency, reduced downtime, maintenance requirements, and the overall cost-effectiveness of the machinery over its lifespan.
Vendor Support and Service: Evaluate thereputation and support provided by the machinery manufacturer or supplier.Consider factors such as after-sales service, technical support, training, and the availability of spare parts. A reliable vendor with good customer support can help ensure smooth operations and minimize downtime.
It's advisable to consult with machinerymanufacturers or suppliers who specialize in cable production equipment. They
can provide detailed information on machine models, capabilities, technical specifications, and customization options based on your specific requirements. Additionally, they can offer insights and guidance based on their industry
expertise to help you make an informed decision.
Max Xu-China wire machinery expert