1. Before start-up, the operator shall check the lubrication, transmission, electrical control and other conditions of all parts of the equipment, and immediately find relevant personnel to solve problems in a timely manner.
2. Select and match the mold according to the product requirements, and adjust the distance between the mold core and the mold sleeve to prevent excessive thickness deviation of the plastic layer.
3. To start the heating system 2-3 hours in advance, adjust the temperature of each section according to the process regulations to prevent the temperature control from being too high or too low.
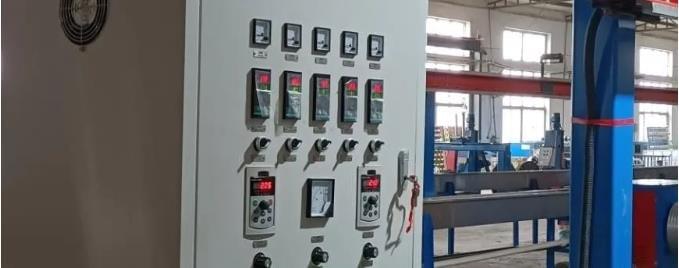
4. Before production, the quality of plastics and semi-finished products shall be checked according to the process regulations, and production can be carried out only after they are confirmed to be qualified.
5. Prepare a suitable take-up reel according to the length of the product, fully consider the bending radius of wires and cables, and arrange the wires firmly and neatly.
6. Prepare the traction rope, test run and observe the screw rotation, traction speed, setting out, take-up and drainage line transmission, heating control system, water supply and drainage flow of each electric switch tank, and start the production after confirming that there is no problem.
7. Start up
1) Put the qualified plastic into the hopper, open the plug plate, start the screw and continue to run the glue. The operator shall pay attention to the feeding condition, and observe the indication of ammeter and voltmeter pointer during glue running. At this time, the operator is not allowed to leave the post to prevent problems.
2) After the plastic is extruded from the mold sleeve, observe the plasticization of the plastic. When the plastic is well plasticized, start to correct the mold, and adjust the plastic thickness evenly to prevent the deviation of the plastic layer.
3) Take samples to check the thickness of the plastic according to the process regulations, and check the quality of the plastic after extrusion, such as pores, surface plasticization, pimples, etc.

4) . After all conditions are normal and the production can meet the requirements of the process regulations, the crew shall be actively organized to start up. During the start-up, the operation shall be divided and closely cooperated.
5). When threading the lead wire and starting the traction, the screw and traction speed shall be controlled according to the thickness requirements of the plastic layer specified in the process, so that the wires and cables can be neatly arranged on the take-up reel of the cable arrangement device after they pass the traction. When threading the lead wire, special personnel shall be assigned to follow the wire connector, and attention shall be paid to prevent water from entering the wire and cable or the connector from being blocked.
6). Check the meter counter to return to the zero position and make the meter accurate. When the wires and cables are reeled, the unqualified joint wires must be cut off, and the thickness and core deviation shall be checked until they are qualified.
7). Pay attention to the following points at any time during the normal production process: product quality, observe and test the surface quality of the plastic layer and the outer diameter of the product at any time; Pay attention to the operation of each part of the equipment; Observe the temperature control of the heating system: pay attention to the change of screw and traction speed to ensure the uniformity of extrusion thickness and product outer diameter; Accomplish "three times", namely, frequently measure the outer diameter, frequently check the quality and frequently observe the equipment; Pay attention to feeding in time to avoid glue breaking, degumming and package leakage; In case of burning during driving, stop the vehicle immediately to clean it; If it is found that the insulation is unqualified and needs to be peeled off, it is not allowed to separate the ends by itself. The glue shall be stopped and the wire core shall be opened to the specified length for treatment to avoid short ends or waste products.
8). Record the process quality of products. Record labels, tracking cards, production reports, process records, etc.
8. Stop machine
When stopping, first cut off the traction current, and then stop the main motor. Open the bolts at the connection between the machine head and the machine body, close the plug plate of the feeding hopper, remove the machine head, and clean the plastic in the cylinder and on the screw. Organize personnel to timely remove the mold core and mold sleeve, and clean the machine head and sieve plate.
1). Stop and clean the machine head in case of the following conditions: stop and clean the machine head in time after production; When the temperature control is too high and plastic scorch occurs, the machine head and screw shall be stopped and cleaned; Clean the machine head after parking for more than one hour; In case of shutdown due to other reasons, such as power failure, water cut-off, waiting for lines, waiting for panels, and equipment and personal accidents, the machine head shall be cleaned.
2). The machine head and screw shall be cleaned, and shall be cleaned in time after cleaning.
3). Keep a shift handover diary and prepare the next shift for production, such as molds, production discs, semi-finished products, etc.
4). Arrange personnel to be responsible for machine cleaning according to post responsibilities.
5). After shutdown, check the power supply, water source, gas source and equipment. After confirming that there is no problem, turn off the power supply, gas source and water source before leaving the machine.