What is the submarine fiber optic cable?
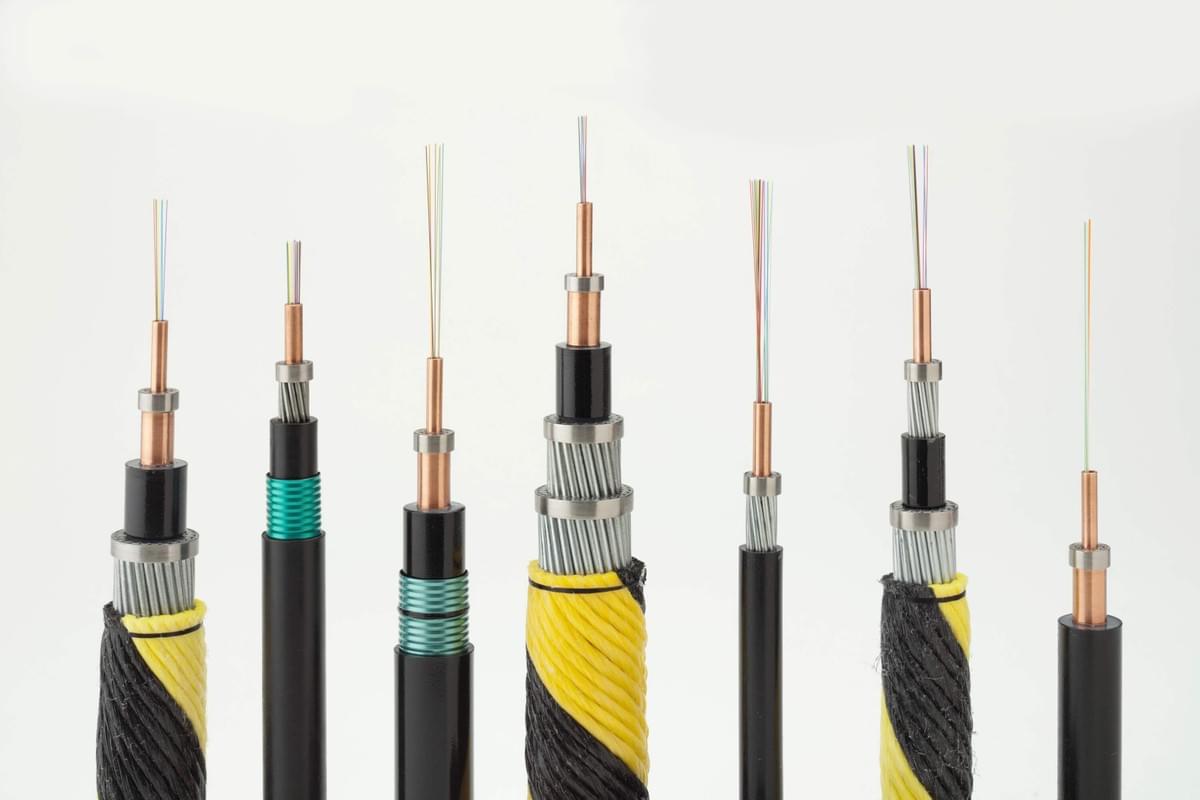
Submarine optical fiber cable, also known as submarine communication cable, is a kind of wire wrapped with insulating material and laid on the seabed to establish the telecommunication transmission between countries.
Submarine optical cable system is mainly used to connect optical cable and Internet. It is divided into two parts: onshore equipment and underwater equipment. Submarine optical cable is the most important and vulnerable part of underwater equipment.
Equipment structure editing
The submarine optical cable is laid on the seafloor with a wire bundle wrapped in an insulating sheath,
Three core submarine optical cable
Three core submarine optical cable
Sea water can prevent the interference of external optical and magnetic waves, so the signal-to-noise ratio of submarine cable is high, and time delay is not felt in submarine optical cable communication. Submarine cables are designed to last 25 years, while satellites typically run out of fuel in 10 to 15 years.
The basic structure of submarine optical cable is: polyethylene layer, polyester resin or asphalt layer, steel strand layer, aluminum waterproof layer, polycarbonate layer, copper pipe or aluminum pipe, paraffin, alkane layer, optical fiber bundle, etc
Submarine optical cable system is mainly used to connect optical cable and Internet. It is divided into two parts: onshore equipment and underwater equipment. The onshore equipment packages and transmits voice, image, data and other communication services. Underwater equipment is responsible for processing, transmitting and receiving communication signals. Underwater equipment is divided into three parts: submarine optical cable, repeater and "branch unit". Submarine optical cable is the most important and vulnerable part.
The structure of deep-sea optical cable is relatively complex: the optical fiber is set in the U-shaped groove plastic skeleton, and the groove is filled with ointment or elastic plastic body to form a fiber core. High strength steel wire is used to wrap around the fiber core. In the process of wrapping, all gaps should be filled with waterproof materials. Then, a layer of copper strip is wrapped around the steel wire and welded to form a joint body of compression and tension between steel wire and copper pipe. The steel wire and copper pipe should be covered with polyethylene sheath. This tight multi-layer structure is designed to protect the optical fiber, prevent fracture and prevent seawater intrusion. In shark infested areas, we need to add a layer of polyethylene sheath outside the submarine cable.
The structure of submarine optical cable requires strong structure and light material, but light metal aluminum can not be used, because aluminum and sea water will produce hydrogen, hydrogen molecules will diffuse into the glass material of optical fiber, which will increase the loss of optical fiber. Therefore, the submarine optical cable should not only prevent hydrogen generation inside, but also prevent hydrogen from penetrating into the optical cable from the outside. Therefore, in the early 1990s, a kind of carbon coated or titanium coated optical fiber was developed to prevent hydrogen penetration and chemical corrosion. The optical fiber joint is also required to be high-strength, which requires that the strength of the original optical fiber and the surface of the original optical fiber are not damaged
Main structure of Submarine Fiber Optic Cable

Which machines are the most important for producing Submarine Fiber Optic Cable?
1. Extrusion machine for outer insulating layer: as shown in the figure above, outer HDPE shear, 3.05 mm thickness, according to this standard, 120 / 25 extruder is required. The main purpose of 120 / 25 is: it is suitable for wrapping the sheath of wires and cables with thermoplastic cable materials such as PVC, PE, XLPE, low smoke and halogen-free.
What kind of 120 extruder can meet the requirements of the outer insulation layer of submarine fiber optic cable? Please see the extruder parameters.
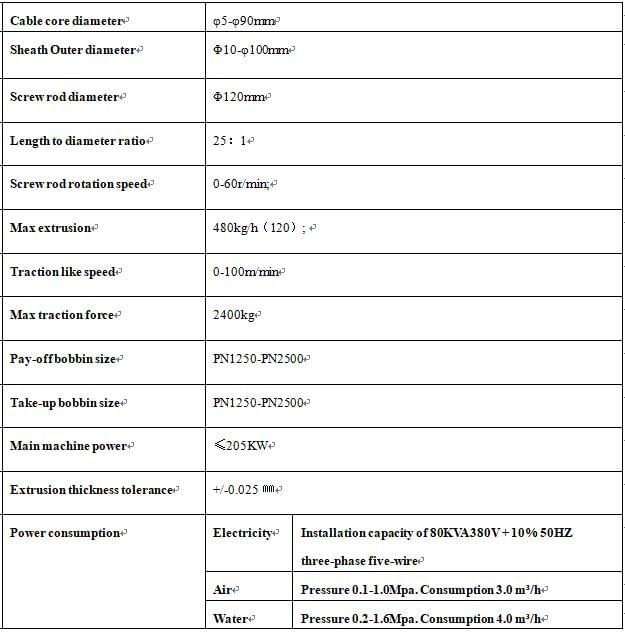
2.Planetary stranding machine for Double Layer Armoring with 3.2mm and 5.0mm Dia. Galvanized Steel Wires:Choose an appropriate armoring machine according to the diameter of galvanized steel strands. The most important point here is the pitch problem, which is also the focus on the quality of Zhuangkai. Because 3.2 and 5.0mm are two different diameter steel wires, the pitch is different when twisted. In this way, the speed of the two layers of 12 steel stranded cages is different. Many companies choose 630/12+12planetary strander. However, because the 5mm steel wire is thick, the 630mm reel will not need to be replaced for a long time, so we recommend the 630/12+800/12 structure .
The following is a brief introduction and technical parameters about planetary strander:
This equipment is mainly used for steel wire armor, and can also be used for control cable, signal cable, small size plastic cable and bare copper, bare aluminum wire stranding.
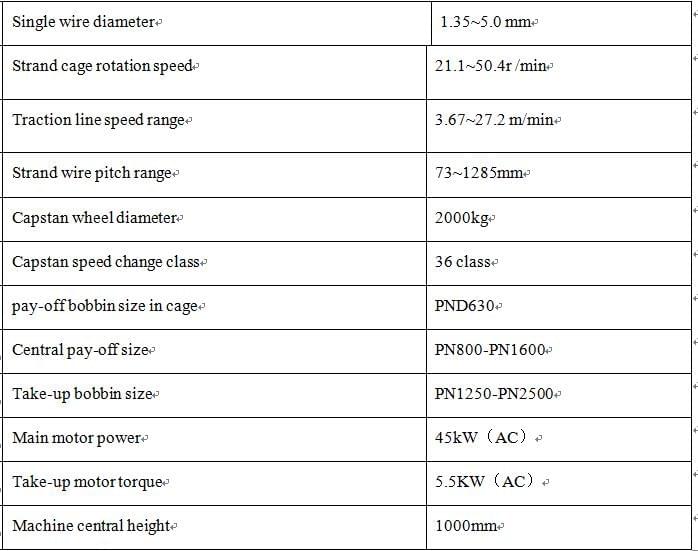
3. 70/25 Cable extrusion line for Inner Polyethylene sheath, 2.6mm Thickness;
The 70 / 25 extruder has a wide range of applications, including ordinary and high-speed models. For submarine optical fiber cable production, as long as the ordinary model can meet the daily production, and the cost is very low.
Use:The unit is suitable for wrapping PVC, PE, PE, XLPE, low smoke and halogen-free thermoplastic cable materials by hot extrusion method for wire and cable sheath.
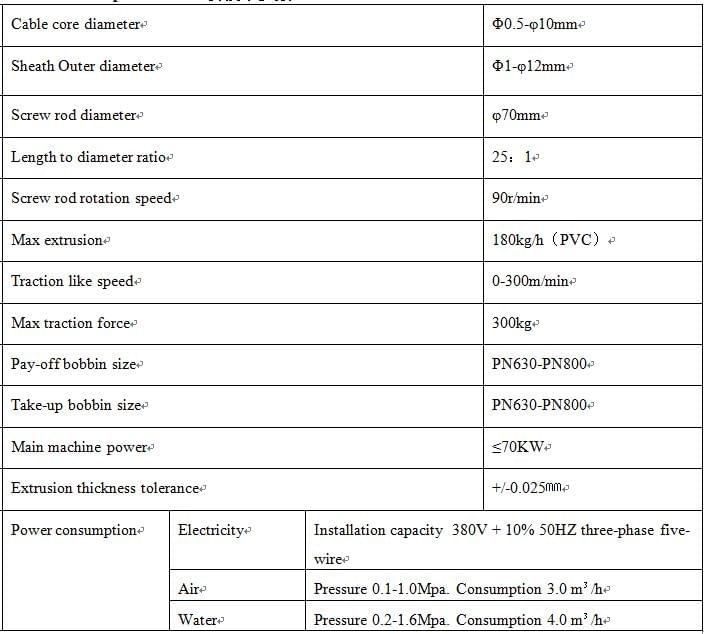
Other machines:
this submarine cable needs asphalt and copper tape shielding. These two machines are very small machines, especially for asphalt laying. They only need to add these functions to the planar strander.
For a factory or supplier in the machinery industry, it is necessary to understand the basic structure of all cables so that the required machinery can be judged.
If you have anything to discuss, please contact me, my email is cabletwister@126.com
Max Xu
Cable Stranding Machine Expert in China
WhatsAPP: +861806615951