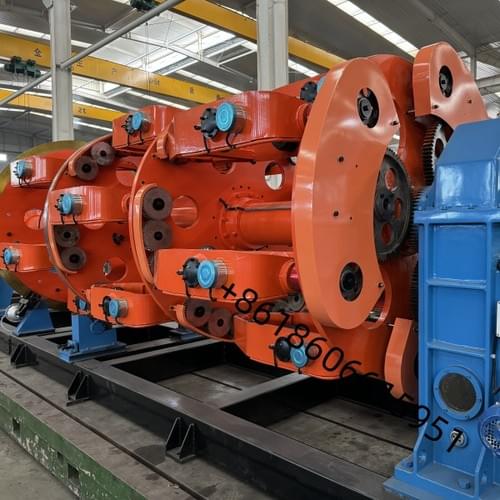
Planetary Closer/Strander JLY400/1+18 With Hysteresis Tension
The machine must be designed for twisting the core of control cables and small-sized cables, with back-twist of the cores, with the simultaneous application of tape insulation along the core.
Planetary Closer/Strander JLY400/1+18 With Hysteresis Tension
DESCRIPTION OF TECHNICAL CHARACTERISTICS OF THE MACHINE
2.1 Twisting elements:
- conductive soft copper conductors (single-wire and multi-wire) with extruded round plastic insulation;
- conductive conductors with plastic insulation, in a screen in the form of a braid made of copper or tinned copper wires.
2.2 Workpiece parameters:
- cross-section of conductive cores: 0.14 – 1.5 mm2;
- diameter of insulated cores: 0.90 – 5.00 mm;
2.3 Number of simultaneously twisted elements - 24 cores.
2.4 Twisting of cores around the central core, diameter: 1.5-25.00 mm.
2.5 Diameter of the finished core by twisting: 2.50-40.00 mm.
2.6 Steps of twisting the layer: 15-1000 mm.
2.7 Tape insulation:
film material - PET, PE, PVC;
- thickness 0.025 – 0.150 mm;
- outer diameter 500 mm;
- inner diameter 76 mm,
- tape width 5-65 mm.
2.8 Maximum speed (by capstan device) – 50 m/min.
2.9 Type of bobbins:
- Pay-off:
a) bobbin with dieter of 400 mm (Appendix 1) or 500 (Appendix 2);
b) for the central core, metal drums according to DIN 46391/46395 1250-1600 mm;
- Take-up: bobbins DIN 46391/46395 with diameter of 1250-1600 mm.
3.1 The design of the machine must ensure:
- Back-twist when twisting into the core;
- installation of pay-off reels weighing up to 150 kg;
- tension when winding the twisted elements from the pay-off reels with smooth adjustment within 0.70-15.0 N;
- change of twisting direction S or Z;
- smooth adjustment of the twist pitch;
- application of 1 or 2 belt insulation tapes on the core by winding, the winding direction must change
3.2 Portal type take-up device:
- metal bobbins according to DIN 46391/46395;
- flange diameter 1250-1600 mm;
- width 900-1200 mm;
- landing hole diameter 56-100 mm;
- availability of replaceable pinoles for landing bobbins of different types;
- maximum weight 5000 kg
4 CONTROL AND MEASURING INSTRUMENTS
4.1 Measuring devices for the number of cage revolutions and the traction speed;
4.2 Automatic electronic (digital) length meter;
4.3 Tape breakage sensors (with machine stop in case of breakage)
5 REQUIREMENTS TO TECHNOLOGICAL ACCURACY
5.1 Twisting speed setting resolution 1 m/min (rpm). Speed maintenance accuracy ± 0.5%.
5.2 Length measurement accuracy 0.2%
6 CONTROL SYSTEM REQUIREMENTS
6.1 Pre-start self-diagnostics and diagnostics of all machine units included in operation and start-up blocking if any unit is not ready;
6.2 Electronic control – PLC, Touch Screen, Inverter f. Siemens.
Symbolic-numeric and text indication on the monitor (display) of the control panel:
- set and current values of process modes;
- messages about the operation of protective interlocks;
- reference information on the operation of individual line units;
- production recipe database.
6.3 Provision of PLC, Touch Screen, Inverter software projects in the latest version after commissioning.
6.4 Table of possible malfunctions, with alarms saved for 7 days.
6.5 The operating manual for the line and for all line components (drives, controllers, operator panels) must be in Russian (or English). Electrical diagrams on paper and in electronic pdf file.