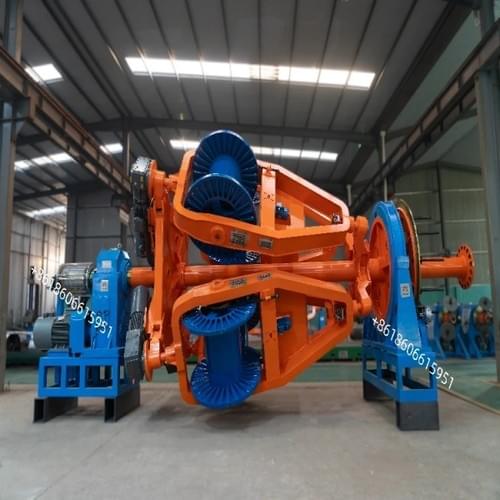
Small Drum Type Cabling Laying Machine CLY-1250/1+4 For Sectorial Cable
Warranty:12 Months
Max Stranding Diameter: 80mm
Cage Speed: 50r/Min
Stranding Pitch: 447~7604mm
Take-up Bobbin: Pn1250~Pn2500
Transport Package: Standard International Shipment Packing
HS Code: 8479400000
Small Drum Type Cabling Laying Machine CLY-1250/1+4 For Sectorial Cable
Advantages
Mechanical friction controls the wire tension, adjustable in size
The bow plate is made of stainless steel, and all wire turns are made with wire wheels, which will not damage the cable surface
Fully enclosed protective cover, axial push-pull structure, safety travel switch protection, with interlocking function with the host
Best after-sales service. Will provide service within 2 days.
Will provide you with professional guidance on how to manage these machines.
Good test quality.
Can twist the cable very quickly. The cage speed can reach 50r/min.
1250/4 bobbin stranding cage
Pay off bobbin size:PN1250
Max load capacity:3T
Max speed:50r/min
Pitch range:200-2500mm (stepless adjustable on touch screen)
Driving motor power: 45KW(AC)
Back twist structure : planetary gear
The winch is operated through the HMI touch screen, and the programmable controller PLC coordinates and controls the start, stop, jog and other operations of the cage.
The Ø1250/4 stranding cage is supported by the reduction box and the large bearing seat. The main shaft is a whole piece of high-quality seamless steel tube, driven by a separate AC variable frequency motor, and has the left and right stranding function. 100% back-twist twisting is realized through the planetary gear mechanism.
The whole machine is designed for high-speed operation, without tugboat load
The back-twist mechanism of the stranding cage adopts planetary gear back-twist, which can withstand large torque.
The cage pre-twisting mechanism is driven by 4 geared motors and can be adjusted online.
The stranding cage is independently driven by a 45KW AC motor with a built-in encoder. The encoder operates in a closed-loop control system and is coordinated and controlled by the programmable logic controller PLC and each unit.
Pay-off tension: The reel frame provides the tension required for pay-off through mechanical belt friction, and the tension can be adjusted manually.
Braking system: winch cage braking through: air pressure brake, frequency converter, braking resistor, etc. are coordinated by PLC to complete the braking process. The entire braking process is synchronized with the whole machine to ensure stable pitch.
There are 12 sets of filling rope pay-off racks at the outlet end of twisted body.
Compared with the tugboat structure, the front support adopts a large bearing, which effectively improves the running speed, is maintenance-free, has low failure rate, and increases the load-bearing strength.